
The Future Landscape of Biosolids Reuse –Building our Resilience
September 7, 2020
Up to 400,000 dry tonnes per annum of biosolids are produced from Australian and New Zealand sewage treatment plants.
Across the globe the last decade has seen a clear trend towards diverting as much biosolids away from landfill as possible, from some countries stopping the agricultural use of biosolids, to others considering alternative treatment to address public concerns over pollutants such as micro-plastics and PFAS.
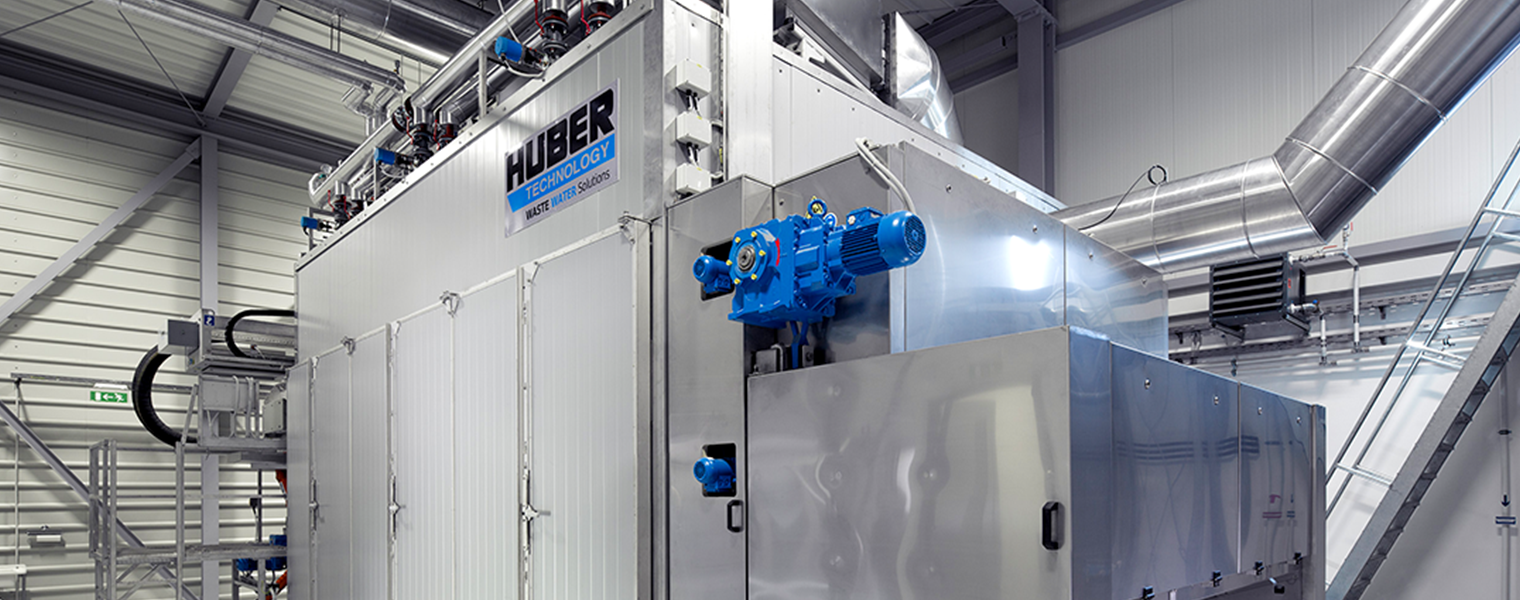
In 2017 Germany banned the agricultural use of biosolids. This action has led to the construction of numerous advanced biosolids facility’s, the majority of which are based on mono-incineration, a process that uses biosolids derived from sewage as a fuel source enabling the generation of power to not only power the incineration plants but also to return energy back to the local domestic grid.
Other markets have looked at alternative solutions such as hydrolysis upstream of biosolids digestion in order to enhance biogas/electricity production and ultimately produce a class A biosolid that can be reused without restriction.
“As the Australian and New Zealand agent for HUBER Technology, we are fortunate to have access to HUBER’s global expertise in the field of biosolids treatment and the role it can play in generating renewable electricity by unlocking its energy potential.” After 10 years of operating their first mono-incineration plant in Straubing Germany, Sludge2Energy, which is a joint venture between HUBER and WTE has now built up its reference base and currently has 6 facilities under construction. Their project at Hanover-Lahe which is due for completion in 2021 will process 130,000 tonnes per annum of biosolids and power up 5000 households.
Whilst mono-incineration and other similar processes are a topic amongst many Australian Water Authorities at a desktop level, lessons learnt into the design and operation of the drying step within the incineration process is something Hydroflux offers the ANZ market in addition to the Sludge2Energy process itself.
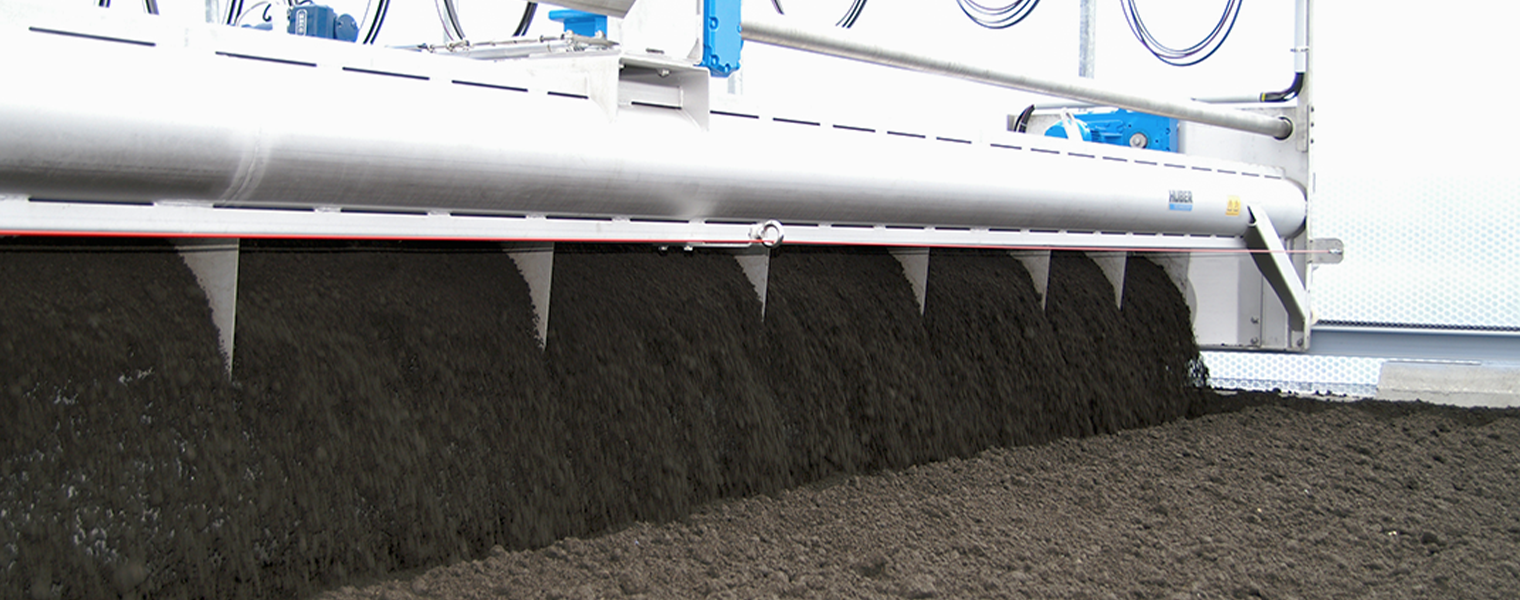
“Partial drying for example, which is producing biosolids with 40% dry solids, can be an ideal intermediate step that bridges the gap between business as usual practice and planning for resilience” says John Koumoukelis, CEO of Hydroflux Epco Pty Ltd. HUBER’s biosolids drying technology includes RotaDry Disc Dryers, BT Belt Dryers and Solstice Solar Dryers.
These technologies rely on a heat source which is typically a waste gas produced within the treatment plant that can be reused. Solstice relies on the sun as the heat source.
Key benefits of drying include reduced transport costs and hence associated carbon emissions, the option for class A biosolids for unrestricted beneficial reuse and future planning for further advanced treatment.
Sludge2Energy is a mono-incineration process that uses a fluid bed furnace to produce renewable energy from biosolids. Hydroflux Epco is a significant driver of ANZ’s future resilience in biosolids handing and disposal with exclusive access to some of Europe’s leading biosolids technology.
Contact Hydroflux Epco at www.hydrofluxepco.com.au for more information.
Up Next
Emerging Contaminants and Other Nuisance Compounds
Hydroflux Utilities Announces Bruce Willis as CEO
Categories
- Tradeshows
- Climate
- Community Engagement
- Corporate Announcements
- Group News
- Newsletters
- Product News
- Project Announcement